CNC Machining of Copper: Navigating Market Trends in Modern Manufacturing
Copper CNC machining is a significantly prominent method in manufacturing that leverages the exact, automatic capabilities of Computer Numerical Control (CNC) technology to generate complex components from copper. Copper's unique properties, consisting of exceptional conductivity, corrosion resistance, and machinability, make it a very popular product in a range of industries such as electronic devices, vehicle, aerospace, and telecommunications. The combination of copper's helpful characteristics and progressed machining techniques makes it possible for makers to produce components with high accuracy and decreased preparation, substantially pushing the borders of advancement. CNC machining permits intricate geometries that would certainly be difficult or difficult to achieve with traditional machining strategies, making it perfect for the manufacturing of elaborate components, such as ports, warmth sinks, and housings.The process of CNC machining requires using a computer to regulate device devices for a more constant and reputable output. This innovation converts CAD (computer-aided design) versions directly into machine-readable code, which overviews the machining process. The result is that suppliers can produce get rid of regular quality and accuracy, lowering waste and the danger of mistake in manufacturing. In the situation of copper, which can be fairly tough to machine due to its thermal conductivity, high ductility, and tendency to work-harden, CNC innovation gives the versatility needed to deal with these worries successfully. Specialized techniques and tools are commonly used to maximize the machining procedure, which can consist of making use of cutting tools coated with hard materials to lessen wear and boost efficiency when dealing with soft steels like copper.
Discover copper cnc machining how copper CNC machining combines advanced technology with sustainable practices to produce intricate, high-precision components, driving development across industries like electronics, automobile, and aerospace.
Among the key benefits of CNC machining copper is the capacity to generate intricate forms that standard machining approaches might not fit. The high precision achievable through CNC technology allows manufacturers to create tightly toleranced features that are crucial in numerous applications. In the electronics industry, for instance, the need for parts with very little tolerances is paramount, as digital tools diminish and much more elaborate. CNC machining facilitates the production of micro-components with such great resistances, allowing improvements in wise gadgets, wearable technology, and other customer electronic devices. Moreover, the repeatability of the CNC machining process ensures that automation of copper components keeps harmony, therefore meeting stringent sector criteria.
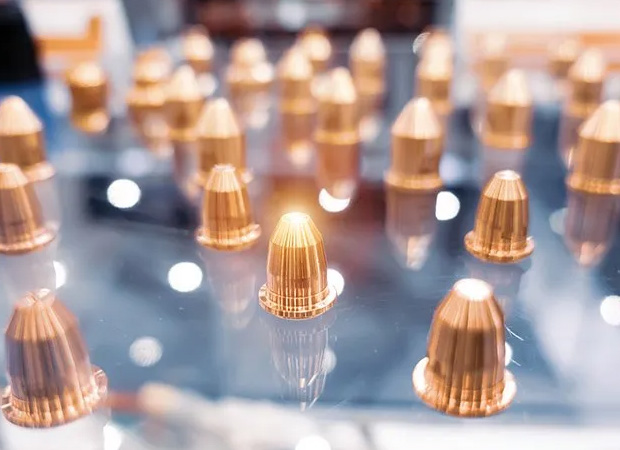
Temperature administration plays an essential duty in the CNC machining of copper due to its capability to conduct warmth rapidly. High-speed machining can lead to substantial warm generation, which may detrimentally impact the buildings of the copper and worsen device wear.
The sustainability element of CNC machining copper is not to be ignored. CNC machining, paired with sustainable methods, can lower waste by allowing producers to use scrap copper from various other processes.
In addition to sustainability, cost-effectiveness is one more vital aspect for makers picking CNC machining for copper parts. CNC machining supplies a reduction in labor expenses due to its automatic nature and decreases the requirement for comprehensive hands-on intervention. In addition, for tiny to tool batch production runs, CNC machining can verify a lot more affordable contrasted to standard machining procedures, as it enables for seamless adjustments and design changes without considerable retooling.
As technology evolves, the capabilities within CNC systems are increasing, additionally improving the capabilities of copper machining. The integration of simulation software allows manufacturers to anticipate possible problems before the machining process begins. These simulations make it possible for far better planning of tool courses and illuminate how the copper material will certainly react throughout the machining process. By identifying and addressing possible difficulties in advancement, companies can decrease downtime and boost productivity, developing a smoother functional flow.
Competent machinists have to be proficient in interpreting layout specs, selecting the proper tools, and readjusting machining specifications to mitigate problems associated with copper's one-of-a-kind machining qualities. Crossbreed machining, which integrates typical CNC machining techniques with additive production, is emerging as a sensible method for producing complex copper parts, blending the staminas of both modern technologies and potentially changing how makers approach copper manufacturing.
In the realm of r & d, CNC machining is helping the expedition of new copper alloys to improve performance additionally. By synthesizing copper with materials such as light weight aluminum, tin, or nickel, makers can engineer composites that have actually improved stamina, electric performance, and resistance to put on and corrosion. These advancements can lead to arising applications in industries that count greatly on conductive materials, such as renewable resource and electric automobiles. As global markets function towards greater energy effectiveness, copper's duty as a conductor in electronic circuits will continue to be extremely important, driving demand for sophisticated machining options.
The aerospace and automobile markets are additionally eager adopters of copper CNC machining, particularly where lightweight components are of vital value. The mix of copper's light-weight nature and excellent electrical and thermal conductivity makes it a perfect option for elements such as electric calls, warmth exchangers, and wiring systems. As the shift toward electric and hybrid cars proceeds, the need for high-performance copper elements will likely rise, therefore thrusting the demand for advanced CNC machining practices that guarantee effectiveness and high quality in production. From a manufacturing perspective, the capability to innovate quickly and provide precision-engineered parts ends up being progressively vital in dealing with the arising needs of these fast-evolving markets.
As CNC machining modern technology remains to establish, it permits additional automation, where fundamental processes such as device adjustments, examinations, and upkeep can be configured into the production cycle. This development indicates that makers will be able to achieve greater performance degrees, much shorter lead times, and higher flexibility in accommodating personalized demands or variants in style. As a result, businesses that involve in CNC machining procedures are better suited to pivot in response to the changes in customer and market needs, promoting growth in an increasingly affordable landscape.
Discover countersink size chart exactly how copper CNC machining merges advanced technology with lasting methods to produce intricate, high-precision parts, driving advancement throughout industries like electronic devices, vehicle, and aerospace.
The worldwide marketplace for CNC machining of copper is observing substantial growth, influenced by aspects such as the rise of clever innovations, electrical vehicles, and recurring efforts to boost power efficiency throughout various applications. In this training, skill and development development continue to be critical; spending in workforce education and learning on CNC machining methods, technologies, and material scientific researches will encourage manufacturers to remain ahead of the contour.
To conclude, the assimilation of CNC machining with copper materials uses a distinctive one-upmanship for suppliers in today's hectic commercial landscape. Its ability to supply high precision, minimize production time, and allow complex layouts makes CNC machining a necessary component of modern-day manufacturing techniques. Combined with sustainability initiatives, cost-effectiveness, and opportunities for advancement, the CNC machining of copper not only fulfills the demands of modern applications yet likewise prepares for the future trajectory of manufacturing in multiple markets. As industries advance and the limits of modern technology expand, accepting CNC machining's possibility will be crucial to realizing unmatched growth and development in the application of copper products. The harmony of copper's product residential or commercial properties with sophisticated CNC machining strategies declares a new age in which sustainability, efficiency, and precision work hand-in-hand to produce cutting edge elements that will certainly specify the future of production and beyond.